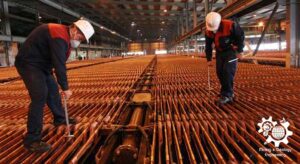
روش های کلی فرآوری مس
روش های کلی فرآوری مس روش مورد استفاده جهت استخراج
سومین مرحله
بخش مهندسی پروژههای معدنی از برداشتهای زمین شناسی، اکتشاف محدوده، مدلسازی ذخیره، مدلسازی اقتصادی، طراحی معدن، برنامهریزی، بهینهسازی و کاهش هزینهها، تولید محصول نهایی و بخش تحقیق و توسعه، اتوماسیون و دیجیتالی کردن در این حوزه است.
معدنکاری که فرآیند استخراج کانیهای با ارزش از زمین است، زمانی به نتایج اقتصادی خود نزدیکتر میشود که ناخالصیهای موادمعدنی از آنها جدا گردد. سلسله عملیاتی که بر روی موادمعدنی انجام میشود تا محصولی با مشخصات قابل قبول در صنعت به دست آید را کانهآرایی یا فرآوری موادمعدنی مینامند.
بار اولیه پس از عملیات فرآوری، محصولی که مشخصات فنی آن مانند عیار، عناصر مفید و مضر، توزیع دانهبندی، کیفیت و کمیت کلیه کانیهای همراه، درصد رطوبت و غیره از سوی مصرف کننده مشخص است به محصول پرعیار شده و یا کنسانتره اطلاق میشود. بقیه مواد، باطله نامیده میشود.
انتخاب و طراحی یک مدار صحیح در مورد یک معدن خاص، یکی از مهمترین و اساسیترین مراحل تصمیمگیری در امر طراحی کارگاه فرآوری مواد معدنی است.
اولین مرحله خردایش و سنگشکنی همان آتشکاری است اگر آتشکاری بهترین شکل ممکن انجام گردد و خردایش سنگ مطلوب باشد علاوه بر افزایش راندمان کاهش هزینه و استهلاک را به همراه خواهد داشت. چرا که خردایش مهمترین قسمت یک کارخانه کانهآرایی را تشکیل میدهند به نحوی که معمولاً 70 تا 90 درصد نیروی مصرفی و 50 تا 70 درصد کل هزینهها را به خود اختصاص میدهد.
به منظور انجام فرآیندهای فرآوری بر روی مواد معدنی ابتدا نیاز است که مواد معدنی تا حد مطلوب در دانهبندی مورد نظر خرد شده و ذرات به درجه آزادی مناسب برسند تا بتوان فرآیندهای فرآوری را بر روی آنها انجام داد. در اثر انجام خردایش ابعاد ذرات کوچک شده و سطوح آنها افزایش میابد. در مرحلهی اول مواد درشت را شکسته و به ابعاد 6-4 سانتیمتری تبدیل میکنند جهت این کار از سنگشکنهای فکی، ژیراتوری و چکشی استفاده میشود.
محصول خارج شده از سنگشکنهای مرحلهی اول ابعاد بزرگی دارد و نمیتوانند مستقیماً به آسیاها یا سایر دستگاههای پرعیار کننده وارد شوند پس محصول به دست آمده را در سنگشکنهای دیگری خرد نموده، به ابعادی در حدود یک سانتیمتر میرسانند برای این منظور از سنگشکنهای مخروطی، استوانهای و ضربهای استفاده میگردد.
نرم کردن نوعی خرد کردن است که طی آن ذراتی که در بین دو سطح قرار میگیرند، نرم میشوند. یکی از مهم ترین اهداف مرحلهی نرم کردن، آزاد ساختن کانی تا ابعاد ذرات باید بین 5/ 0 الی 1/ 0 میلیمتر برسد. عمل نرم کردن مواد در دستگاه هایی به نام آسیاها انجام میشود محصول خارج شده از سنگشکنهای مرحلهی دوم پس از کنترل دانهبندی توسط سرندها به آسیاها وارد میگردد. آسیاها به دو روش خشک و تَر کار میکنند.
سرند کردن، طبقهبندی مواد به روش مکانیکی است و بر مبنای ابعاد ذرات و احتمال عبور و یا توقف آنها در سطح سرند استوار است. از سرندها برای طبقهبندی مواد درشتتر از 250 میکرون است استفاده میشود.
در طبقهبندی غیرمستقیم که توسط کلاسیفایرها انجام میپذیرد مواد براساس ابعاد، جرم مخصوص طبقهبندی میکنند. به معنای دیگر مواد را براساس اختلاف سرعت ته نشینی در یک سیگنال معین، طبقهبندی میشود؛ و در واقع از حرکت جامدات در داخل سیالات و اختلاف مقاومتها و سرعت دانهها در این حرکت، برای تقسیم بندی آنها استفاده میگردد. کلاسیفایرها به دو نوع اصلی آبی و خشک تقسیم میشوند که انواع مهم از این دستگاه شامل کلاسیفایرهای ناودانی، مخروطی، مکانیکی، پارویی و مارپیچی است
کاربرد هیدروسیکلونها در مدار خرد کنندهها و به جای کلاسیفایرهای مکانیکی، به خصوص وقتی که دانههای آسیا شده ابعادی کمتر از 150 میکرون داشته باشند، با ارزش است. در شناورسازی برای جدا کردن دانههای کوچکتر از 15 میکرون، به خصوص در شستشوی «کائولین» به کار میروند. به علاوه از سیکلونها در جدا نمودن گل حفاری از ذرات شن در چاههای نفت و یا برای جدا نمودن ذرات الماس از شن نیز استفاده میکنند.
یکی از مهمترین کاربردهای آن در کنترل بار در گردش در مدار آسیاهاست. به عبارتی محصول آسیاهای گلولهای پس از خروج از آسیا وارد هیدروسیکلون شده و محصول ریزتر از حد لازم از سرریز وارد مدار فلوتاسیون شده ولی مواد دانه درشت از تهریز هیدروسیکلون مجدداً وارد آسیا میشود که به آن بار در گردش گفته میشود.
جیگ ظرف روبازی پر از آبی است که به وسیله یک سرند افقی به دو قسمت تقسیم شده است. بار ورودی از دریچه فوقانی جیگ وارد شده و از دریچه دیگر مواد سبک سرریز میشوند. دریچه قسمت تهتانی نیز برای تخلیه مواد سنگین تعبیه شده است. مکانیزم عملکرد جیگ با استفاده از تزریق آب با فشار یا دمش هوا و یا حرکت پیستون و دیافراگم در داخل محفظه جیگ یک حرکت نوسانی در آب (یا هوا) ایجاد میشود که باعث ایجاد جهش و کشش بر روی مواد شده و در نتیجه موجب جدایش مواد بر اساس وزن مخصوص میشود.
از میز برای پرعیارسازی مواد دانهریز و در بعضی موارد برای پرعیارسازی موادی که با سایر روشهای ثقلی پر عیار نشدهاند استفاده میشود. همچنین از میز به عنوان یک روش پیش فرآوری برای بعضی نمونه ها مانند سنگ آهن، منگنز، سرب، روی و... استفاده میشود.
میز از یک سطح شیبدار تشکیل شده است که بر روی آن تعدادی مانع وجود دارد. در امتداد طول میز جریان آبی عمود بر جهت لرزش میز وجود دارد. مواد معدنی از گوشه بالایی میز وارد آن میشوند. بر این اساس مواد سنگین با توجه به وزن مخصوص خود در کف میز قرار گرفته و نمیتوانند از موانع عبور کنند. اما مواد سبک به کمک جریان آب از موانع عبور کرده و به قسمت باطله منتقل میشوند. مواد سنگین که در پشت موانع روی میز قرار گرفتهاند در اثر لرزش میز به جلو رانده شده و در نهایت از قسمت کنسانتره خارج میشوند.
فرآوری موادمعدنی با استفاده از خاصیت مغناطیسی در قرن اخیر جایگاه ویژهای پیدا نموده است بخصوص در مورد جدایش کانیهای آهن دار نظیر مگنتیت، هماتیت و لیمونیت از باطلههای همراه و همچنین جدایش کانی اسفالریت از پیریت صورت میگیرد. از دیگر استفاده این نوع جدایش، جدا کردن قطعات آهنی است که ممکن است ناخواسته وارد مادهمعدنی شده باشند. هزینه نگهداری و تعمیر این دستگاهها زیاد نبوده و بازدهی آنها هم بالا است.
برای استفاده از دستگاههای جداکننده مغناطیسی اولین شرط این است که ماده معدنی خاصیت مغناطیسی داشته باشد. در ابتدا از این دستگاهها برای جدا کردن موادی که خاصیت مغناطیسی قوی داشتند استفاده میشد اما با ساخته شدن جدا کنندههای مغناطیسی قوی تر امروزه از این دستگاهها برای کانیهای با خاصیت مغناطیسی کم نیز استفاده میشود.
فرآوری و جدایش در میدان الکتریکی براساس دادن بار الکتریکی به موادمعدنی میباشد. برای این نوع جدایش یا موادمعدنی را در مجاورت میدان الکتریکی، قطبی میکنیم و یا در اثر اصطکاک باردار مینماییم. البته میدان الکتریکی فقط از اجسام عایق عبور میکند. در این نوع اجسام الکترون آزاد وجود ندارد اما در اجسام هادی یک یا چند الکترون آزاد در حرکتندو به وسیله جریان الکتریکی جا به جا میشوند. خاصیت متفاوت اجسام که همان قدرت انتقال الکترونها در جسم است عامل اصلی جدایش در میدان الکتریکی است. بر این اساس اجسام به سه دسته هادی، نیمه هادی و عایق تقسیمبندی میشوند.
جداکنندههای الکتوراستاتیکی دو نوعاند نوع اول دستگاههای الکترواستاتیکی با میدان قوی و نوع دوم دستگاههای الکترواستاتیکی با میدان صعیف هستند. جدایش ذرات در جداکنندههای الکترواستاتیکی هنگامی میسر است که بار ذرات و مسیر حرکت ذرات مختلف باشد. مسیر حرکت ذرات نه فقط به نیروی الکتریکی، بلکه به نیروی جرکی یعنی نیروی ثقل و گریز از مرکز هم بستگی دارد. در این نوع جدایش ذرات در در جداکننده استوانه الکترواستاتیکی به حرکت در میآیند. ذراتی که کاملا عایق هستند در میدان الکترواستاتیکی فقط قطبی میشوند و نیروی جاذبه مابین استوانه و ذره بسیار کم است و در نتیجه مسافت بیشتری را بر روی استوانه حرکت خواهد کرد. اما در ذرات هادی بین استوانه و ذرات فورا یک نیروی الکتریکی دفع کننده و یا جذب کننده ایجاد میشود.
فلوتاسیون یکی از روشهای فرآوری و آرایش مواد معدنی است که بر مبنای خواص شیمی فیزیکی سطوح جامدات برای ذرات 20 تا 200 مش در یک محیط سیال و جریان هوا برای ایجاد حبابهای مناسب بنا شده است. در فرآیند فلوتاسیون ذرات جامد در آب تشکیل پالپ میدهند و ذرات بر اساس خواص شیمیایی و فیزیکی سطوحشان طی فرآیند فلوتاسیون با چسبیدن به حباب هوا جداسازی میشوند. فرآیند فلوتاسیون که عمدتا برای کانیهای سولفیدی بکار میرود به دو روش مستقیم و معکوس صورت میگیرد که در روش فلوتاسیون مستقیم کانی و و عنصر هدف به سطح سلول فلوتاسیون آمده و باطله در ته سلول میماند اما در روش معکوس کانی و عنصر هدف به ته سلول رفته و باطله به سطح سلول میآید.
برای انجام فرآیند فلوتاسیون از موادی نظیر کلکتور (برای آبران کردن سطح کانی به منظور چسبیدن به حباب هوا)، بازداشت کنندهها (به منظور آبدوست کردن سطح کانی برای ماندن در ته سلول)، تنظیم کنندهها (به منظور تنظیم pH)، متفرق کننده (به منظور متفرق کردن ذرات ریز و نرمه)، کف ساز (برای پایدار سازی حباب هوا) و فعال کنندهها (به منظور آماده کردن سطح کانی برای آبران شدن توسط کلکتور) استفاده میشود. در فرآیند فلوتاسیون برخی کانیها نظیر، گرافیت، زغال، الماس و مولیبدن،گوگرد و تالک ذاتا آبران بوده و نیاز به کلکتور ندارند. تجهیزات فلوتاسیون میتواند به دو صورت سلول مکانیکی و یا ستونی باشد که در سلول مکانیکی تجهیزات مکانیکی نظیر همزن وجود دارد اما در سلول ستونی همزن و تجهیزات مکانیکی وجود نداشته و حباب هوا توسط جریان توربولنتی تولید میشود.
لیچینگ فرآیند استخراج یک جز محلول در جامد با استفاده از یک حلال میباشد. در این رابطه یکی از دو هدف زیر قابل دستیابی خواهد بود:
1- تجزیه کانه، کنسانتره یا محصولات برای محلول کردن فلز موجود در آن
2- لیچینگ ترکیباتی از یک کانه یا کنسانتره که به آسانی قابل حل باشند جهت تولید کنسانتره با غلظت زیاد. به عبارت دیگر بهرهوری شیمیایی از یک کانه
انتخاب عامل لیچینگ جهت محلولسازی کانهها به پارامترهایی نظیر حلالیت، هزینه، مواد و تاسیسات، عملکرد انتخابی عامل لیچینگ و بازیابی بستگی دارد.
آب یکی از عوامل لیچینگ مناسب است که هم ارزان و هم غیرخورنده است اما برای تعداد محدودی از کانیها کاربرد دارد. غیر از آب عوامل لیچینگ شامل اسیدها، بازها، محلولهای آبی نمکها و آب کلر هستند.
عوامل اسیدی لیچینک عمدتا شامل اسید سولفوریک، اسید کلریدریک و اسید نیتریک هستند. عوامل بازی لیچینک نسبت به عوامل اسیدی گرانتر بوده اما مشکلات مربوط به خورندگی را نداشته و همچنین عملکرد انتخابی بیشتری دارند. همچنین از عوامل بازی زمانی استفاده میشود که باطله برخی کانیها میل ترکیبی شدیدی با اسیدها داشته و با بازها کمتر ترکیب میشوند. از عوامل بازی لیچینگ میتوان به هیدروکسید سدیم و هیدروکسید آمونیوم اشاره کرد.
از دیگر عوامل مهم لیچینگ میتوان به تیزاب سلطانی و سیانید اشاره کرد که در فرآیند انحلال طلا بکار گرفته میشوند. تیزاب سلطانی مخلوطی از اسیدنیتریک و اسید کلریدریک بوده که توسط جابربن حیان کشف شده است.
اولین تلاشها در کاربرد فرآیند تبادل یونی برای بازیابی فلز، در مورد بازیابی مس از محلول باطله کاپرآمونیوم رایون و صنعت برنج، بازیابی نقره از باطلههای حاصل از فیلمهای عکاسی و بازیابی کروم از باطلههای آبهکاری بود. اورانیوم اولین فلزی بود که به وسیله روش تبادل یونی در مقیاس بزرگ از محلولهای لیچ بازیابی شد.
فرآیند تبادل یونی برای عمل آوری محلولهای خیلی رقیق به ویژه برای محلولهای با غلظت یون فلز حدود 10ppm یا کمتر مفید میباشد. عموما این روش برای محلولهای با غلظت یون فلز بیش از یک درصد مفید نیست. تبادل یونی در سنگها، شنها، خاکها، شیشه، چوب، پشم، پارچه و دیگر مواد، رخ میدهد.
روش استخراج با حلالهای آلی یک فرآیند شیمیایی است که در این روش فلزات موجود در فاز آبی برای تشکیل کمپلکس آلی فلزی با یک ماده آلی واکنش میکند و لذا اجزای فلز آبی را ترک کرده و وارد فاز آلی میشوند. فلز در فاز آلی با اتمهای کربن به صورت ترکیباب آلی فلزی پیوند ندارد ولی با اکسیژن، نیتروژن، گوگرد و یا هیدروژن با یک پیوند کوئوردینانسی(داتیو) ارتباط دارند. واکنش شیمیایی عکس روش استخراج را استریپینگ میگویند.
روش استخراج با حلال آلی برای اولین بار در هیدرومتالورژی در پروژه منهتن برای تولید بمب اتمی به کار رفت. یک کارخانه صنعتی نیز برای تهیه محلول نیترات اورانیل با خلوص بالا در آمریکا ساخته شد.
این روش به تدریج برای فلزات گران قیمت مانند، پلوتونیوم، توریوم، نیوبیوم، تانتالیوم، زیرکنیوم، هافنیوم، برن، برلیوم و نهایتا مولیبدن با بهبود روشهای مذکور ادامه یافت. مرحله دوم در دهه 1960 اتفاق افتاد زمانی که روش استخراج با حلال برای اولین بار برای استخراج فلز نسبتا ارزان مس به کار رفت. در حال حاضر، تکنولوژی روش استخراج با حلال آلی دارای گسترش وسیع، مقبولیت خوب و راندمان بالایی است.
فیلتراسیون به عملیات جدایش مایع از جامد اطلاق میگردد که به طرق مختلف قابل انجام میباشد.
در کارخانههای ذوب کنسانترههای معدنی را به فلزات خالص تصفیه میکنیم. جریان ساده و فرآیندهای پایدار به ما این امکان را میدهد تا تولید هر دو فلز و محصولات جانبی را در یک استراتژی که دامنه وسیعتری از محصولات، باطلههای باقیمانده کمتر در تولید و افزایش رقابت را فراهم میکند، به حداکثر برسانیم. در کارخانههای ذوب با فرآیندهای مختلفی از جمله ذوب، تکلیس، لیچینگ، تصفیه و الکترولیز مواد را از هم جدا مینمایند.
کارخانههای ذوب ایران عمدتا شمش سرب و روی، شمش آلومینیوم، کاتد مس، شمش سرب، گرانول طلا و نقره و سایر محصولات مانند اسید سولفوریک، کلینکر روی، دی اکسید گوگرد و کنسانتره پالادیوم تولید میکنند.
در سنگهای ساختمانی نظیر تراورتن، گرانیت، مرمر و...، و سنگهای تزئینی همانند الماس، یاقوت، زمرد و... پس از استخراج مثل سایر موادمعدنی احتیاج به مراحل پیچیده جهت رساندن آن به بازار مصرف ندارند.
پس از استخراج آنها به کارگاه برش سنگ منتقل میکنند و در آنجا توسط دستگاه برش به صورت یک دست و موازی برش داده میشوند و به ابعاد مورد نظر میرسند پس از آن بسته به نیاز با دستگاه تراش به اشکال مختلف و زاویههای خاص در میآورند پس از انجام این مرحله بسته به میزان درجه سختی سنگ توسط سایندههای مخصوص مورد صیقل و سایش قرار میگیرند و در انتها در صورت نیاز به منظور بالا بردن مقاومت آنها روی آنها یک لایه رزین ریخته میشود.
پس از انجام تمامی مراحل معدن کاری و فرآوری به دلیل مسائل زیست محیطی مواد باطله باقی ماده به محلی به نام سد باطله منتقل میشوند که سد باطله طبق روشهای مختلف و استاندارد طراحی میشود. مقاوت مکان سد باطله باید به گونهای باشد که در برابر عوامل طبیعی مقاومت کرده و شکسته نشود زیرا در غیر آن صورت خطر انتشار مواد جامد، سمی و اسیدی در محیط زیست، محل زندگی انسان و همچنین آبهای زیرزمینی وجود دارد. این سدها طوری کف سازی میشوند و در کف سازی از موادی نظیر رس به منظور جلوگیری از نفوذ مواد سمی به داخل آبهای زیرزمینی شود.
اگر باطلهها حاوی گوگرد بود و تشکیل زهاب اسیدی دهند در سد باطله از مواد کربناته و آهکی به منظور خنثی سازی خاصیت اسیدی مواد باطله استفاده میشود. اگر مواد باطله از نوع رادیواکتیویته باشند عمدتا آنها را در گنبدهای نمکی به دلیل خاصیت خودبندی نمکها دفن میکنند. از روشها و تکنولوژیهای نوین حذف باطله از معادن روش گیاه پالایی است که در آن مواد سمی و باطله توسط انواع خاصی از گیاهها جمع آوری شده و به مکان دیگری منتقل گشته و یا تثبیت میگردند.
روش کنترل مواد باطله و نوع ساختار شد باطله بستگی به نوع مواد باطله، محل قرار گیری مواد باطله، شیب معدن، درجه بندی ریسک مواد باطله موجود، رادیواکتیویته و غیر رادیواکتیو بودن مواد، زلزله خیزی و طوفان خیزی محیط قرارگیری باطله، اسیدی و غیر اسیدی بودن مواد و دیگر عوامل بستگی دارد.
پر عیار کردن سنگ آهن با جدا کننده مغناطیسی ر